Verifying the chemical composition and metallurgical properties of raw materials used for black iron gas pipe fittings production involves several steps and quality control measures.
Here’s how it is typically done:
- Supplier Qualification: Before raw materials are procured, suppliers are thoroughly evaluated based on their reputation, reliability, and adherence to quality standards. Suppliers should provide material certifications and documentation detailing the chemical composition and metallurgical properties of the materials they supply.
- Material Certification: Suppliers provide material certifications, which include information such as chemical composition, mechanical properties, heat treatment details, and compliance with relevant standards (e.g., ASTM, ASME). These certifications serve as official documentation of the raw material’s quality and compliance with specifications.
- Chemical Analysis: Samples of raw materials are collected and subjected to chemical analysis using techniques such as spectroscopy (e.g., X-ray fluorescence, optical emission spectroscopy) or wet chemical methods. This analysis verifies the elemental composition of the materials and ensures that they meet specified requirements.
- Metallurgical Testing: Metallurgical testing is conducted to assess the microstructure and mechanical properties of the raw materials. Techniques such as metallography, hardness testing, tensile testing, and impact testing are employed to evaluate properties such as grain size, tensile strength, yield strength, elongation, and impact resistance.
- Non-Destructive Testing (NDT): Non-destructive testing methods, such as ultrasonic testing, magnetic particle testing, or dye penetrant testing, may be used to detect surface and subsurface defects in the raw materials without causing damage. black iron gas pipe fittings These tests help identify any flaws or discontinuities that could affect the integrity of the finished pipe fittings.
- Sampling and Inspection: Random samples of raw materials are selected for inspection to ensure representativeness and consistency. These samples are inspected visually for surface defects, dimensional accuracy, and conformity to specifications.
- Quality Assurance Procedures: Quality assurance procedures are implemented throughout the manufacturing process to monitor and control the quality of raw materials at each stage. This may include inspection checkpoints, process controls, and documentation of test results to ensure traceability and accountability.
- Statistical Process Control (SPC): Statistical process control techniques are used to monitor key process parameters and identify any deviations from established control limits. SPC helps maintain consistency and reliability in raw material quality by detecting and correcting variations in real-time.
- Supplier Audits: Regular audits and assessments are conducted to evaluate the performance of raw material suppliers and ensure ongoing compliance with quality standards. Suppliers are expected to demonstrate their commitment to quality management practices and continuous improvement.
- Certification and Compliance: Once the raw materials have been verified to meet all specified requirements, they are certified for use in production. Certificates of compliance are issued to document the testing and verification process, providing assurance of the raw materials’ quality and suitability for manufacturing black iron gas pipe fittings.
By implementing these comprehensive verification processes and quality control measures, manufacturers can ensure that the raw materials used for black iron gas pipe fittings production meet the required chemical composition and metallurgical properties, resulting in high-quality and reliable products.
How is the overall performance of black metal pipe fittings assessed under different operating conditions?
The overall performance of black metal pipe fittings is assessed under different operating conditions through a combination of testing, inspection, and evaluation methods. Here’s how this assessment is typically conducted:
- Pressure Testing: Pipe fittings are subjected to pressure testing to evaluate their ability to withstand internal pressure under various operating conditions. Hydrostatic pressure testing involves pressurizing the fittings with water or another suitable fluid to a specified pressure level and monitoring for leaks or deformations.
- Temperature Testing: Pipe fittings are tested at different temperatures to assess their performance under thermal stress. Thermal cycling tests involve subjecting the fittings to alternating hot and cold temperatures to simulate temperature fluctuations during operation. This helps evaluate the fittings’ dimensional stability, material integrity, and resistance to thermal expansion and contraction.
- Corrosion Resistance Testing: Pipe fittings are tested for corrosion resistance to assess their durability and longevity in corrosive environments. Accelerated corrosion tests, such as salt spray testing or exposure to corrosive chemicals, simulate the effects of corrosion over time and help identify any weaknesses in the fittings’ protective coatings or surface treatments.
- Mechanical Testing: Mechanical testing is conducted to evaluate the strength, ductility, and structural integrity of pipe fittings under different loading conditions. Tensile testing, bending tests, and impact tests assess the fittings’ ability to withstand external forces, bending moments, and impacts without failure.
- Sealing Performance Testing: Pipe fittings with threaded or flanged connections are tested for sealing performance to ensure leak-tightness under pressure. Sealability tests involve pressurizing the fittings with a sealing medium (e.g., air, water) and checking for leaks at the joints or connections.
- Flow Testing: Flow testing assesses the hydraulic performance of pipe fittings by measuring pressure drop, flow rate, and velocity through the fittings under various flow conditions. This helps evaluate the fittings’ resistance to flow restrictions, turbulence, and pressure losses, ensuring efficient fluid conveyance.
- Dimensional Inspection: Dimensional inspection verifies the dimensional accuracy and conformance of pipe fittings to specified standards and tolerances. Measurements of thread dimensions, wall thickness, bore diameter, black metal pipe fittings and overall dimensions are taken to ensure proper fit, alignment, and compatibility with other components in the piping system.
- Material Analysis: Material analysis techniques, such as chemical analysis and metallurgical examination, are conducted to verify the composition, microstructure, and material properties of pipe fittings. These tests ensure that the fittings are made from suitable materials with the required mechanical strength, corrosion resistance, and durability.
- Environmental Testing: Pipe fittings may be subjected to environmental testing to assess their performance under extreme conditions, such as exposure to UV radiation, moisture, chemicals, or environmental contaminants. This helps identify any degradation or deterioration in the fittings’ properties over time.
- Field Performance Monitoring: In addition to laboratory testing, the performance of black metal pipe fittings is monitored in real-world operating environments to assess their long-term reliability, functionality, and maintenance requirements. Field performance data, feedback from end-users, and failure analysis help identify any issues or improvements needed in the fittings’ design or manufacturing.
By conducting comprehensive testing and evaluation under diverse operating conditions, manufacturers can ensure that black metal pipe fittings meet performance requirements, comply with industry standards, and provide reliable and safe operation in various applications.
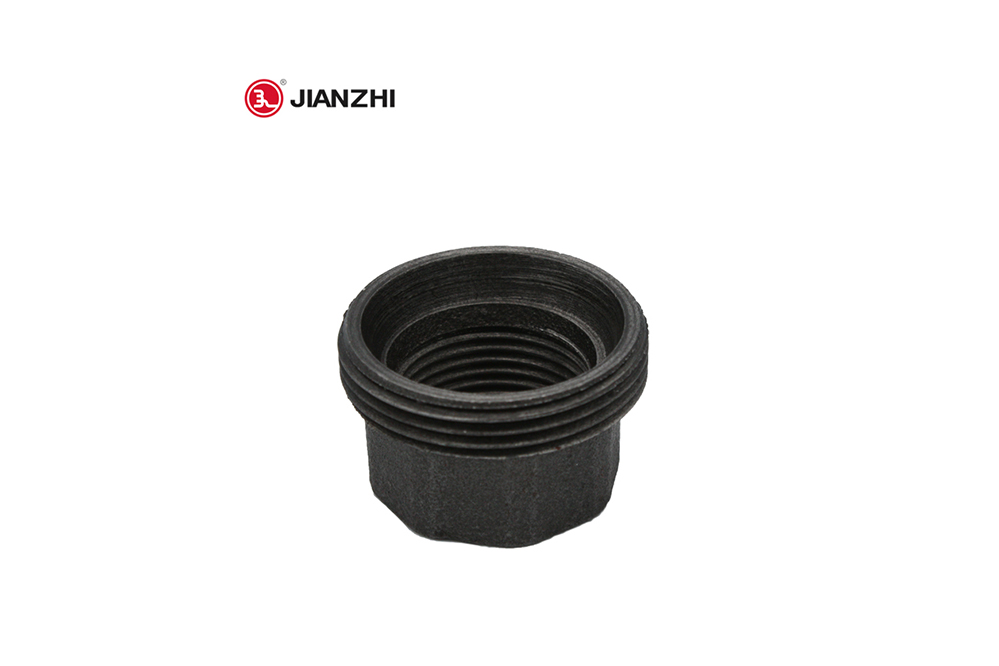