Cast and forged black iron pipe compression fittings serve similar functions in plumbing and piping systems but have differences in their performance characteristics due to variations in manufacturing processes and material properties.
Here’s a comparison of the performance differences between these types of fittings:
- Manufacturing Process:
- Cast Fittings: Cast black iron pipe compression fittings are made by pouring molten iron into molds and allowing it to cool and solidify. This process produces fittings with intricate shapes and complex internal configurations.
- Forged Fittings: Forged black iron pipe compression fittings are manufactured by shaping heated metal billets under high pressure using forging dies. This process creates fittings with superior strength and durability.
- Material Properties:
- Cast Fittings: Cast black iron fittings may have slight variations in material composition and properties due to the casting process. While cast fittings offer good strength and durability, they may have some inherent porosity or internal defects that can affect performance.
- Forged Fittings: Forged black iron fittings have a more uniform and dense grain structure, resulting in superior strength, toughness, and resistance to internal defects. Forged fittings are less prone to cracking, brittleness, or failure under high-pressure conditions.
- Strength and Durability:
- Cast Fittings: Cast black iron fittings offer adequate strength and durability for many plumbing and piping applications. However, the presence of internal defects or porosity may reduce their load-bearing capacity and longevity compared to forged fittings.
- Forged Fittings: Forged black iron fittings are known for their exceptional strength and durability. The forging process aligns the grain structure of the metal, resulting in fittings that can withstand higher pressure, temperature, black iron pipe compression fittings and mechanical stress without deformation or failure.
- Corrosion Resistance:
- Cast Fittings: Cast black iron fittings may be susceptible to corrosion over time, particularly in humid or corrosive environments. Proper coating or surface treatment may be necessary to enhance corrosion resistance.
- Forged Fittings: Forged black iron fittings may have better corrosion resistance than cast fittings due to their denser grain structure and uniform composition. However, both types of fittings may require additional protection against rust and corrosion, such as galvanizing or painting.
- Cost:
- Cast Fittings: Cast black iron fittings are generally more cost-effective than forged fittings due to the lower production costs associated with the casting process.
- Forged Fittings: Forged black iron fittings are typically more expensive than cast fittings due to the higher production costs associated with forging and the superior performance and durability they offer.
In summary, the performance differences between cast and forged black iron pipe compression fittings primarily stem from variations in manufacturing processes, material properties, strength, durability, corrosion resistance, and cost. Proper selection of fittings based on the specific requirements of the plumbing or piping system is essential to ensure optimal performance and longevity.
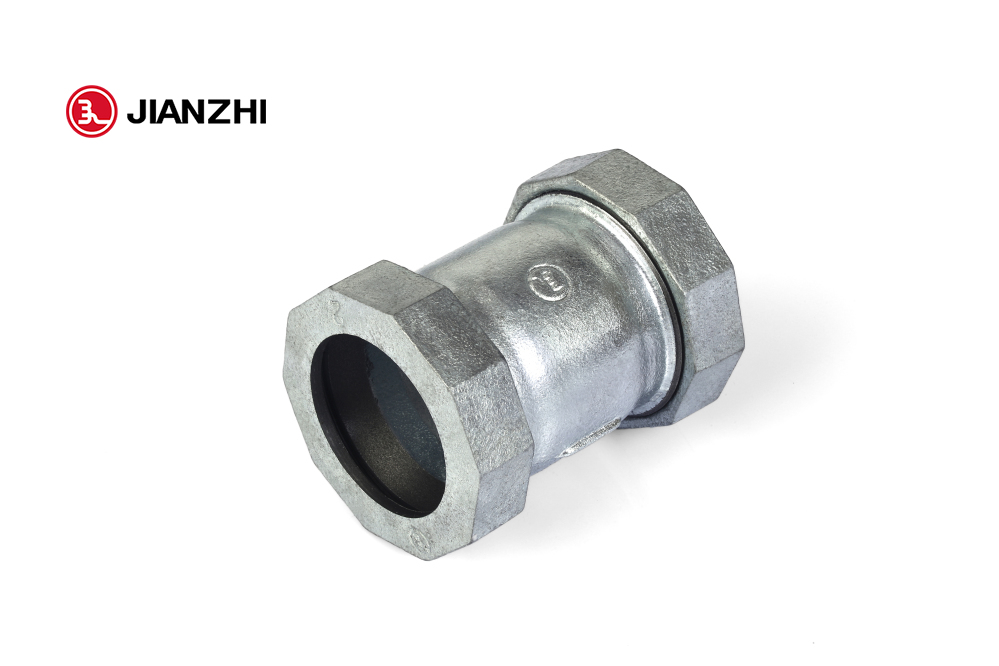